overview of the project
builder: stryker europe
construction volume: 58’000 cubic meters
total floor area: 7’500 square meters
average costs per square meter: 1'951 CHF
average costs per cubic meter: 261 CHF
situation
stryker was considering buying and reconstructing an existing production plant in the la chaux-de-fonds region. They compiled a list of requirements and created a detailed schedule. There were to be administration offices, storage and production spaces as well as contamination-free.rooms mühlemann + partner were chosen as the planning team in charge and were assigned with carrying the project into execution. the team undertook an in-depth cost estimation and discovered that an entirely new building would result in a much better cost-benefit ratio. a new construction was then planned on another plot of land arranged by the cantonal business development department. the site was located in close proximity to the local airport, which was taken into account when designing the construction and working out the details of the building process.
solution
because of building
restrictions limiting the height of the
construction due to air traffic, the building was designed to combine
all the required elements on a single floor. warning lights also had to
be placed on the roof.
as always when it comes to designing industrial buildings, the team of
architects and planners created rooms that display a high degree of
flexibility and functionality. mounting rigs were placed on the
outsides of production halls so that less supporting pillars were
needed on the inside., making it easier to adapt to changing needs.
infrastructure facilities were located to the roof. the specific choice
of building materials was made to minimize overall maintenance.
production halls, contamination-free rooms and their respective offices
are in the northern most part of the factory, whereas administration
premises are to the south. this way, a future step-wise expansion to
the north should pose no problems whatsoever.
despite the large size of the building, its appearance remains elegant
and light, thanks to the great work of the architects. it corresponds
well to the high-tech products produced by stryker. the southern face
of the building is equipped with fixed, sturdy sun blinds. because of
the weather conditions in these regions, the use of regular blinds was
not possible. mühlemann + partner made clever use of the
blinds though to round off the building’s architecture.
the tight schedule - first talks were held at the end of february in
2004, building commenced in march of the following year and the
hand-over was scheduled for november 2005 - was able to be held due to
highly efficient work flow.
the project is a perfect example of how a clients’ ideas can
be improved upon and implemented in dialogue with an experienced team.
technical as well as aesthetic specifications were met and the project
was able to be completed within the approved budget and on schedule.
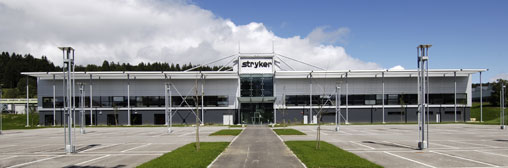
![]() |
![]() |
![]() |
![]() |